What are the best materials for sustainable construction and renovation?
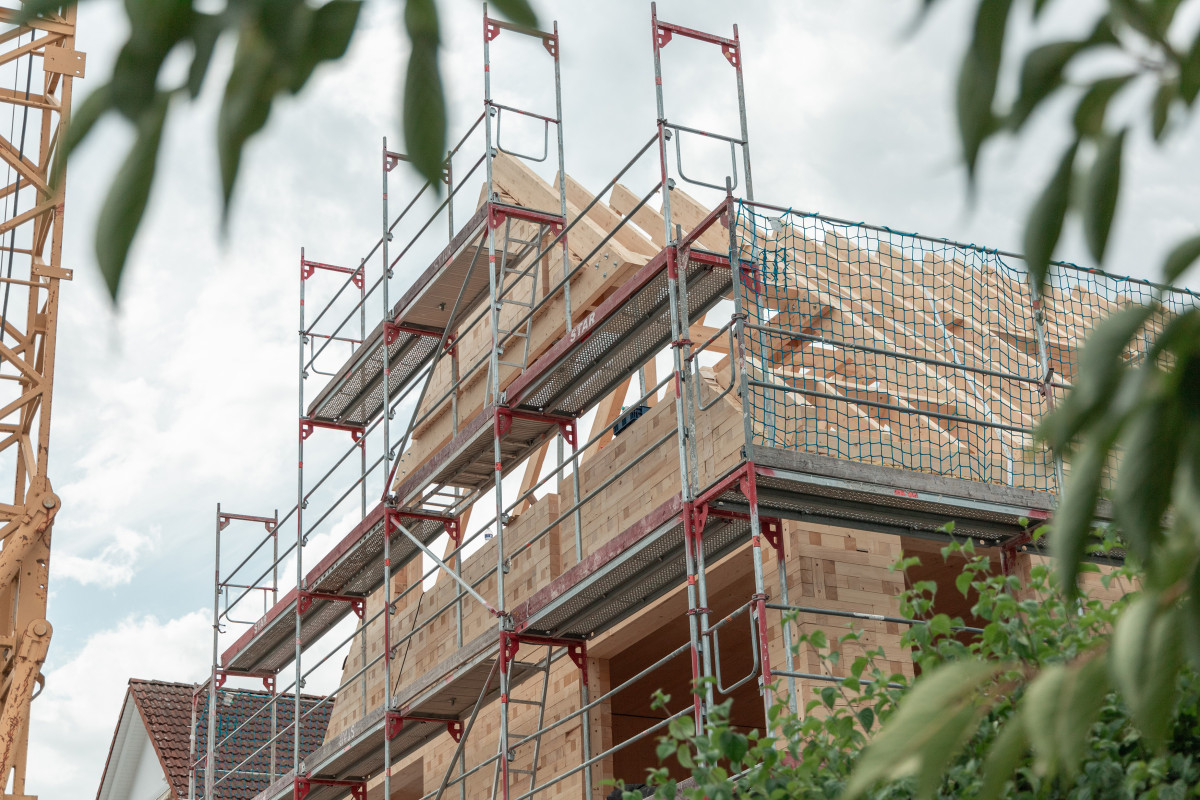
***Please note: This factsheet is part of CLEW's deep dive into embodied carbon, published in collaboration with FORESIGHT Climate and Energy. Find all publications in our dossier 'The construction sector's struggle to go from big polluter to carbon hero'.***
Traditional construction materials like cement or steel come with a large environmental price tag, adding to the building sector's climate performance. Currently, most decarbonisation efforts are focussed on reducing emissions from heating, cooling and lighting. This is set to change as Europe's buildings become more energy efficient, gas and coal heating is replaced, and electricity generation made cleaner.
In fact, looking at buildings' carbon footprints throughout their entire lifecycle – from the manufacture of their materials to their demolition – the OECD expects the share of emissions embodied in construction materials to be just as high as operational emissions by 2050. In the most extreme cases, embodied emissions already make up more than 90 percent of a building's carbon footprint.
What materials are chosen to build with is critical towards determining – and limiting – the full climate impact of offices, shops and houses.
This is because the production of today’s most widely used construction materials often is very polluting. "Just three materials – concrete, steel and aluminium – are responsible for 23 percent of overall global emissions today," a 2023 UN Environment Programme (UNEP) report states. In Europe, construction accounts for 250 million tonnes of CO2 emissions every year.
More sustainable construction materials exist, but they tend to be costlier and builders often distrust them. Still, developers and architects are increasingly using nature-based alternatives, such as timber, clay and even hemp, in their projects. At the same time, many manufacturers are finding ways to green up their products. What materials can homes, schools and restaurants be made of in a net zero future?
Bringing sufficiency and efficiency into the equation
Avoiding new construction altogether is generally the most sustainable option: Extending the lifetime of existing buildings, making better use of them and re-using their components and materials when they have to be deconstructed is the single option likely to save the most emissions, limit resource extraction and cut waste.
"We need to think about growth and consumption in general," Kim Gundlach, architect and researcher at the Natural Building Lab (NBL), told Clean Energy Wire (CLEW). In many places, including Germany, it is often easier to demolish and re-build rather than adapt or refurbish an existing building.
At the same time, researchers agree that Europe's building stock is not used to its full potential. "It's really important that we continue to use the spaces that we already have and make them fit for further use," Angelika Drescher, researcher and project manager at think tank Bauhaus Earth, told CLEW.
Using materials that have already been manufactured is one of the lowest-hanging fruits to decarbonise new construction and renovation projects. There is tremendous potential to re-use materials already present in our built environment, especially in developed economies with a large and ageing building stock, according to UNEP.
For new buildings, researchers say that both designing efficiently with fewer materials (which can be achieved while retaining the same structural strength) and taking a closer look at existing building standards that might conflict with climate neutrality targets should be more prominent in the discussion to make buildings more sustainable.
"Climate-just design and construction principles should be integrated in the curricula of universities," Gundlach said. "We need highly qualified people in this sector to meet the tasks of tomorrow."
Shifting to bio-based materials
Constructing with bio-based materials would allow the building sector to go from significant polluter to carbon hero. Materials such as timber, bamboo, straw or hemp all capture carbon as they grow. Schools, homes and offices built using these materials could store more carbon than their construction emitted in the first place, and thus make them carbon sinks over the buildings' entire lifespans, which usually cover at least several decades.
"It is about duration and about storage," Bauhaus Earth's Drescher said. "If stored CO2 in a 100- year-old-tree stays in a building for longer than 100 years, then we have managed to delay its release and help the atmosphere breathe a little."
The shift to (properly managed) bio-based materials could lead to emissions savings of up to 40 percent in many of the world's regions by 2050, even compared to savings from low-carbon concrete and steel, according to UNEP's 2023 report. At a European level, the construction sector could reduce emissions by 18 percent by 2030 if 50 percent of new residential construction shifted to bio-based materials, circular economy consultancy Metabolic found.
However, "The economic incentive is just not strong enough for a lot of people to actually work with these materials," NBL's Grundlach said. In Germany, for example, this is due to very complex building certification and permitting processes, as well as issues of liability and warranty, especially for re-used materials and non-standardised products.
"There is a knowledge gap between research, industry and politics that needs to be overcome by qualitative collaboration between different stakeholders," she added.
Still, there is progress: since 2022, France requires all new public buildings to be constructed with at least 50 percent timber or other natural materials, while municipalities in Greater Amsterdam agreed that, by 2025, at least 20 percent of new constructions should use wood as a primary material.
It is important to make construction processes much more flexible and adaptable, Bauhaus Earth's Drescher said. "We do not know what materials will be available in future climatic conditions. Therefore, we need to strengthen regional value chains for more regional resilience: smaller structures may be able to adapt much more organically."
Timber
Mass timber (engineered wood, such as cross-laminated timber) can compete with steel and reinforced concrete in building structures. It holds great potential as a sustainable construction material and already is widely used in projects today. Timber could help society reach climate targets: a cubic metre of wood contains around one tonne of carbon, depending on the tree species.
Among its many benefits, mass timber is highly durable, fireproof, and building components can be pre-fabricated off-site in a modular or serial way, reducing construction waste and speeding up building processes. Wood is also light, making it ideal for adding stories to existing buildings, which creates living areas without sealing up more ground. Moreover, it is an effective insulator, reducing the need for heating and cooling.
However, just how climate friendly wood products are depends on the extent of sustainable forest strategies and responsible felling, as well as on broader social and ecological contexts. Trees take a long time to grow and the resilience of forests to climate change is an important factor for their productivity.
"There's a lot of research into how the construction sector can deal with different types of wood, such as hardwood, because we simply don't know which trees will grow in future and whether forests will continue to grow as vigorously as they do now or whether they will have problems with droughts," Bauhaus Earth's Drescher said.
According to UNEP's 2023 report, 38 percent of the world’s wood products are used in the built environment (roughly 1,800 million tonnes in 2020). A 2020 report by the Potsdam Institute for Climate Impact Research (PIK) found that, in theory, the world could harvest enough timber to construct 90 percent of new buildings with the material by 2050. However, sustainable forest management is key, and uncertainties remain, the authors warned.
"To focus on timber as a building material is important. However, instead of new buildings we need to focus on renovations and extensions and work with the existing building stock," NBL's Gundlach argued. "Also, other nature-based materials as well as hardwood materials are important for a climate-just construction sector."
Similarly, Anna Braune, head of research and development at the German Sustainable Building Council (DGNB), argued that timber construction is not the ultimate solution. "There's a desperate attempt to continue with business as usual except with wood, but we can't continue with business as usual with so much new construction," she told CLEW.
"We need to seriously consider how much surface area we have across Europe – there is increased competition for land use for construction, for energy production, for agriculture, for biodiversity protection. To continue with our business models, but just with wood, is not sustainable in the long run." This also applies on a global scale: "For most countries in the world, a timber-only solution is neither possible nor desirable," a 2020 report in journal One Earth concluded.
Focusing on re-used timber is a largely unexplored option, while lower grades of timber or by-products that are generally burnt for biomass could find other purposes, including wood-fibre insulation. The start-up TRIQBRIQ in southern Germany, for example, is developing building blocks made out of waste wood that would otherwise be shredded into chipboard or burnt. They are locked together like LEGO blocks and can be completely reused at the end of a building's service life.
Clay
Already a popular construction material in many parts of the world until not too long ago, clay is experiencing a renaissance as a sustainable alternative to conventional building materials. Clay buildings are environmentally friendly, sound-insulating, non-combustible, and the material generally is locally available.
Clay is used in ceilings, walls, roofs and floors, as well as for panels in drywall construction, and clay plasters are also common. Pressed or moulded into bricks, clay (or rammed earth) can also have immense load-bearing capacities.
This type of construction remains experimental, but lighthouse project ProtoPotsdam, southwest of Berlin, used excavated clay, which is generally disposed of as expensive waste, for part of its load-bearing structure.
The project developers standardised and certified the unbaked compressed clay bricks, and in the process they found – "to their own astonishment" – that the bricks could be used to build up to five storeys high structures (for many years, load-bearing clay walls were only permitted in Germany in buildings up to two storeys high). Bauhaus Earth also found that, compared to conventional building materials such as sand-lime bricks, bricks or concrete blocks, clay blocks have a 10 to 20 times lower CO2 footprint.
Clay has great temperature and moisture-regulating properties, and also has a positive effect on room acoustics and room climate. However, the material is sensitive to weather: the ProtoPotsdam project halted construction in winter, as clay must not be exposed to frost to retain its qualities. This means building with clay requires different construction processes, but Bauhaus Earth's Drescher, who oversees the project, argues that these changes are part of what makes the transition to sustainable materials exciting.
Other nature-based materials
Other natural materials, such as bamboo, grasses, straw or hemp, can already cover buildings' envelopes and insulation needs. They are not only more sustainable than most conventional materials but, when used properly, buildings constructed with bio-based materials can even benefit the health of residents, from better indoor air quality to increased creativity.
A waste material from grains, straw is being rediscovered as a valuable insulation or panel material. It has high heat insulation and good sound insulation properties, and is highly resistant to moisture and mould when processed properly. Using it as a building material does not generally require additional cultivation areas; the share that is not used for animal husbandry in Germany, for example, would be enough to insulate 350,000 single family homes, according to the information platform Gebäudeforum klimaneutral.
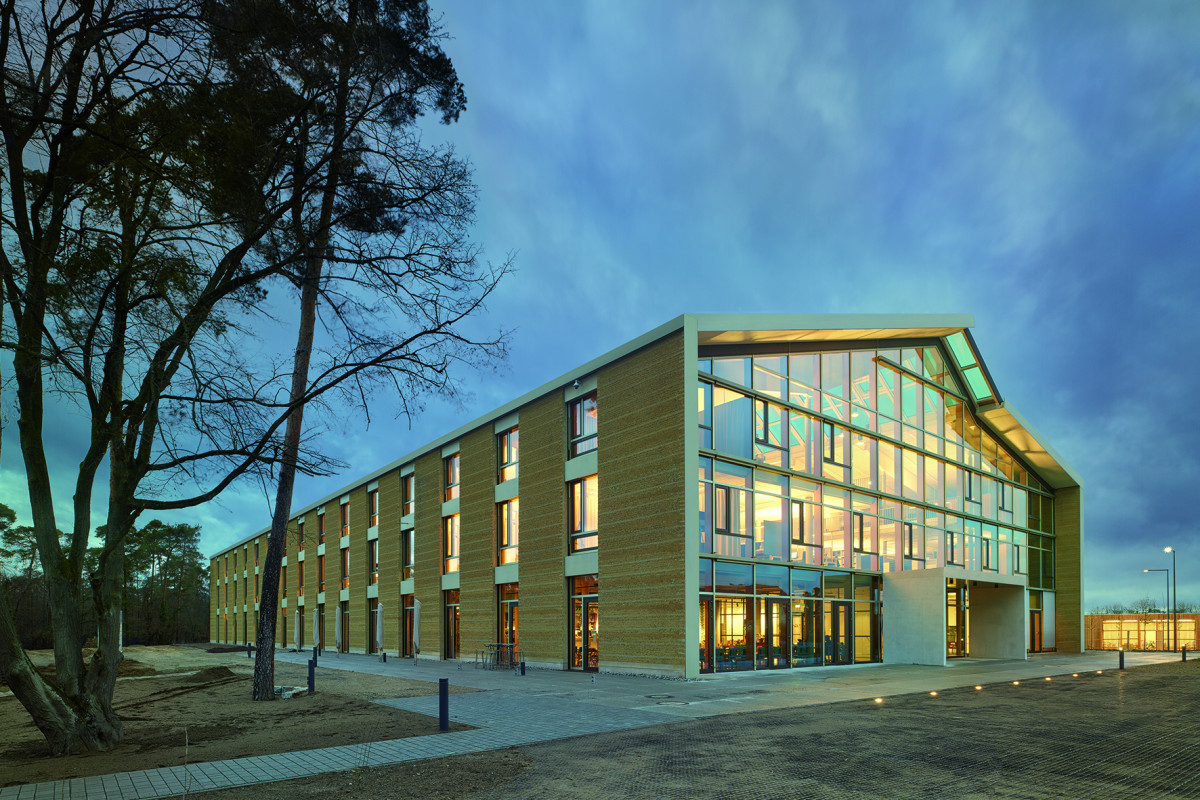
As exemplified by a sports centre near Paris, the use of hemp as a building material is also promising. The plant grows quickly and hardly requires pesticides. It can be used as an alternative to aluminium and steel panels or, more notably, as "hempcrete", a non-load bearing wall and insultation material. Hemp varieties cultivated today in Europe can store between 7 and 9.6 tonnes of CO2 equivalent per year, a report commissioned by the European Industrial Hemp Association (EIHA) found.
"Innovation doesn't automatically mean it needs to be new and fancy," Fabian Hörmann, author and founder of regenerative architecture firm YR22, told CLEW. "Good old materials like earth, straw or hemp can replace carbon-intensive materials for some sections of buildings. The key is to put each material in the best place in a construction to benefit from its specific advantages."
Still, innovation and new technologies do open the door to more solutions. Academics in the Netherlands are researching the potential of making ceilings and flooring out of fungi, as mushrooms grow fast and have excellent physical properties as a construction material. Meanwhile, researchers in Denmark, Australia and the UK are exploring the potential of algae, seaweed and shellfish, which do not compete for land use and are generally pest-resistant.
Given that the EU expects the vast majority of its building stock to still stand in 2050, insulation materials to increase the energy efficiency of leaky homes and offices will be of crucial importance to reach climate neutrality. Natural insulation materials (such as cellulose, produced mainly from waste paper, or regionally grown flax, cork, reed and paludicultural crops) are not necessarily inferior to synthetic insulation materials. Still, they currently have significantly lower sales volumes.
Low-carbon cements
Cement and concrete are by far the most prominent building materials, comprising 70 percent of Europe's total buildings' mass. Cement is the second most used material in the world after water.
There is a good reason for this, Brant Walkley, senior lecturer and head of the sustainable materials research team at Sheffield University, told CLEW. "The performance of cement is exceptional and has allowed us to build modern society," he said. "We have now realised that, like many revolutionary technologies, it is damaging in many ways, but the material itself is quite amazing."
Portland cement is the most widely used type of the material, although its production is inherently polluting. The chemical reaction of converting limestone, its main component at around 90 percent, into clinker releases carbon (750-850 kg for every tonne of cement) – there is no way around that. Six to eight percent of global emissions can be attributed to the cement industry – a share higher than that of global aviation.
This is not to say that the carbon footprint of cement cannot be reduced: Changing the materials used for concrete production (using blended cements and alkali-activated materials, more below), as well as altering designs to use much less cement (a University of Stuttgart project, for example, developed concrete with pores or cavities in areas of low loads, saving up to 40 percent of material used) and re-using existing components are all ways to improve the sustainability of the industry as a whole.
Another solution that big cement companies in Europe are investing heavily in is carbon capture technologies. This is "the only known pathway" to bring cement's emissions close to zero, according to the World Economic Forum. The EU has presented a proposal for industrial carbon management and the German government has proposed plans to make carbon capture and storage (CCS) possible to help the country reach greenhouse gas neutrality by 2045.
However, many open questions remain, including cost hikes (current production costs increase by between 50% and 85%), and a lack of carbon transport and storage infrastructure. "Carbon capture and storage is not currently viable for mass uptake for cement production and I don't know if it ever will be," Sheffield University's Walkley argued.
Several types of lower carbon cements are used in industry, but none at the scale that would meet demand. "I don't see that changing dramatically anytime soon," Walkley said, going on to explain that there is a huge amount of capital in existing infrastructure to make traditional Portland cement, and that poses a big challenge. "Most sustainable cements that have taken off are those that have not needed to change any of that infrastructure."
How can material changes reduce cement and concrete's carbon footprint?
- Blended cements: Blended cements like Limestone Calcined Clay Cement (LC3 cement) use supplementary cementitious materials such as fly ash or blast furnace slag (which are industrial waste materials) and mix them with traditional Portland cement at different percentages, cutting the amount of carbon-intensive clinker required. They are used at scale by industry today, as this material mix can both improve sustainability and modulate properties, such as how fast the cement sets.
- Alkali-activated concrete: This type of cement-free concrete uses supplementary cementitious materials like blast furnace slag or fly ash along with an alkaline activator, such as sodium hydroxide or potassium silicate. They emit at least 40 percent less carbon than ordinary Portland cement. The challenges for their widespread uptake are not necessarily technical, Walkley said. They have more to do with supply chain logistics, achieving the scale of production required to meet current demand for cement and concrete, as well as political or entrenched focuses.
Note that “sustainable cement” is a slippery term, and that global warming potential only addresses carbon emissions and not other environmental impacts, such as water and resource use.
"There is no single solution to decarbonise the cement sector, but there are many options available, and all of the ways to reduce carbon emissions will be necessary and used to some extent, depending on the application," Madeline Rihner, a Sheffield University PhD researcher assessing the industry's decarbonisation strategies through life cycle assessments, told CLEW.
Demand for cement and steel is only set to increase in the coming decades as the world's population and cities grow. "The question is not can we replace cement and concrete with something else, it is how do we make it more environmentally friendly and sustainable," Sheffield University's Walkley said. "I would be cautious in saying that we can achieve climate neutrality or net zero, but I am very optimistic that we can make huge progress."