Reused and recycled buildings challenge wasteful construction status quo
***Please note: This article is part of a series on the climate and environmental impact of construction, published in collaboration with FORESIGHT Climate and Energy. You can listen to a version of it here and find the full series here.***
The CRCLR House in Berlin looks almost unfinished even though it was completed in 2022. There is no paint on the walls, which are a mix of timber, clay, hemp and what was left from the brewery that once stood there. Every joint is visible, as is the wiring running along the walls.
The idea behind the project: When, decades down the line, the time comes for the space to be changed to serve a different purpose, the building can be taken apart like a LEGO house, with the individual components retaining their original form and quality, ready to be used again.
As the name suggests, the co-working space was built following circularity principles. Around 70 percent of its materials were produced sustainably or were previously used elsewhere: from the bathroom sinks reclaimed from a camping site and timber from an art installation now converted into meeting booths to windows and fire safety doors.
“Form followed availability,” commented Felix Hauerken from Impact Hub, the organisation providing the co-working spaces. Construction started before the building plan was fully finalised, and the design was adapted as materials from demolition sites or carpentry workshops became available.
Where reclaimed or “waste” materials were not available, the project developers used low-carbon ones. Above the shared offices, the architects added affordable flats. The new stories are made out of timber and insulated with straw – all materials screwed or wedged to make their eventual deconstruction as smooth as possible.
Finite resources, yet a mountain of waste
About half of the raw materials extracted in Europe every year end up in buildings and roads. Yet, these resources are finite: There are more materials now embedded in buildings and infrastructure than are easily accessible in the earth, said Rebekka Steinlein, architect and business development manager at Concular, a circular construction business.
Construction and renovation sites alone also generate over a third of the waste that ends up in Europe's landfills. Globally, 13 percent of materials delivered to construction sites are sent directly to landfill without being used at all, according to the World Green Building Council (WGBC).
The current linear system does not work and needs to change.
Beyond finite resources and mountains of waste, there is the question of emissions. The EU estimates that greenhouse gas emissions from material extraction, manufacturing of construction products, and the construction and renovation of buildings account for 5 to 12 percent of total member states' emissions. As a result, the bloc’s building stock has emerged as a key obstacle to reaching the EU’s goal of climate neutrality by 2050, enshrined as a legal obligation in its Climate Law.
Less is more
A circular approach, which disconnects economic activity from the ever-increasing consumption of natural resources, has emerged as a key strategy to overcome this dilemma. Circularity recognises the value of used materials by keeping them in supply chains, rather than discard them into landfill. Applying these principles to buildings means constructing houses with reclaimed, low or zero-carbon materials in such a way that they can be recovered and reused in future projects.
There is a hierarchy to circularity beyond the idea of keeping materials and components in "infinite" use cycles. It prioritises prolonging the value of buildings for as long as possible, followed by reusing their materials, rebuilding old ones to be as good as new – a process known as remanufacturing – and recycling or downcycling as a last resort, followed ultimately by incineration or disposal.
However, "designing efficiently often gets left out of the circularity discussion," said Danielle Densley Tingley, a senior lecturer in architectural engineering at the University of Sheffield. Construction projects often use more materials than needed. For example, it is often possible to retain the same structural strength with only 50 to 60 percent of the cement used today. This alone has the potential to save 1 billion tonnes of CO2 per year by 2050, according to a 2023 report.
Indeed, shifting to a circular built environment could reduce global carbon emissions from building materials by 38 percent by 2050, thanks to reduced demand for new steel, aluminium, cement and plastic, a 2019 report by the Ellen MacArthur Foundation found.
"The most sustainable building is the one you don't build”
Circularity first and foremost encourages extending the lifespan of existing buildings. "The most sustainable building is the one you don't build,” said Sheffield University's Densley Tingley. “Changing our attitudes and massively increasing re-use of buildings within Europe is probably going to be the single most effective way of reducing carbon."
Her views were echoed by her Sheffield University colleague Dr Charles Gillott, a construction expert. "We need to dramatically prioritise retention of existing buildings over demolitions and deconstruction," he said. "There is huge circular potential within the existing building stock as it currently stands."
"You could build the most circular or lowest carbon building possible, but if you demolished something that was in its place in order to be able to do so, that isn’t actually a good thing overall,” he added.
Prolonging the lifetime of existing buildings has the potential to reduce emissions by an additional 1 billion tonnes of CO2 per year beyond 2050. Repurposing existing buildings – opening office canteens as restaurants in the evening, or converting unused office space (which has grown in the aftermath of the COVID-19 pandemic) – is one way to achieve this, according to the European Environment Agency (EEA), an EU advisory body.
What are our buildings made of, exactly?
If the materials embedded in buildings are to be reused, we need to know what, and where, they are. This is a huge challenge for circularity today: With very few exceptions, we simply do not know what the walls around us and the floor we’re standing on are made from.
Poor design and lack of information mean that, globally, only 20 to 30 percent of construction and demolition waste is recycled or reused.
While the concept of urban mining has picked up – the notion of finding, extracting, reusing or recycling materials already built into urban areas – there is still no requirement to either assess the re-usability potential of materials inside of buildings being demolished today, or to document what materials go into new buildings or refurbishment projects.
"Even nowadays, when we build, we do not document it," said Dominik Campanella, one of Concular's co-founders. "There's no digitalisation, meaning that after one year, for most buildings the whole documentation no longer exists."
Digital tools like Building Information Models (BIM) and so-called resource passports are bridging this gap, especially in the Nordic countries. The former are "digital twins" of buildings, serving as a central database during a building's entire lifecycle, while the latter register essential information about the product they belong to (composition, origin of resources, global warming potential, quality, deconstructability), enabling comparison between materials, and meaning resources can be used by multiple actors across different value chains.
Business as usual not an option
Despite EU efforts to boost circularity across the bloc, progress is slow. A recent EEA report pours cold water on the notion that Europe has widely embraced circular economy principles: “Europe continues to operate under a predominantly linear model, where products placed on the market tend to have a relatively short use phase,” it states. “Business models primarily revolve around mass-producing products, often sacrificing quality, and this results in early breakdown or premature obsolescence.”
Indeed, a 2023 report identified a lack of attractive circular business models as one of the primary barriers to greater circularity. This is particularly true for buildings: Their long lifespan means that a share of the profits of building in a circular way will only pay off decades down the line.
The market for material recovery – current demolitions – can also be challenging: 85 percent of Europe’s buildings were erected over 20 years ago, meaning they might contain toxic materials, such as asbestos. Many materials are glued together rather than bolted, making it hard to separate and salvage them.
Still, there is tremendous economic as well as ecological value embedded in salvaged materials. But many project developers are oblivious of this and are stuck in their habits. A change in business models is needed if circular economy approaches are to be adopted at scale, according to ARUP’s Vangsbo.
“Circular economy needs to be viewed as a business strategy, not just a waste management or a design strategy,” he said. “If a critical mass of investors and construction clients embraces this message, we are confident the real estate sector can deliver significant returns, while reducing its negative burden on the planet.”
For those used to the status quo, adopting a new production mindset can be difficult. But doing so is a necessity if companies want to become fit for a climate neutral future, said Lars Autrup, CEO of the Danish Architects Association.
“Business as usual is not a solution. Unfortunately, far too many businesses are extremely conservative and will fight against any form of change,” he added.
Regulators play catch-up
Autrup argued that government policy should be used to shift the construction sector towards circularity, including taxes on carbon emissions, life-cycle assessment requirements, and the use of Environmental Product Declarations (EPDs) to ensure long-lasting materials are favoured.
In doing so, we can achieve a Europe-wide shift, where our built environment is seen as "a resource to be reused at its highest level of conservation," Autrup said. In other words: viewing buildings as valuable "material banks", instead of single-use structures.
Regulation to encourage circular design and building practices is picking up, especially at EU level. This includes the European Taxonomy, the European Performance of Buildings Directive (EPBD) and the Construction Product Regulation (CPR).
"It's good to have something in place, but if we really want to tackle climate change then the measures are not enough," Concular's Campanella said, explaining that most regulations still focus on virgin materials – a minimum quota of recycled materials in production, for example – but not much exists for reclaimed materials themselves.
"Regulation is the key. But having a way to measure circularity in buildings is also important," Campanella added. While the circular performance index is a recognised industry standard, giving buildings a score up to 100, what counts as circular is measured differently across the EU.
Reporting on circularity and circularity-related environmental topics is difficult, as frameworks and benchmarks don’t always exist or align.
More than half of new buildings in Europe meet less than 50 percent of the requirements of a circular economy, according to a 2023 report by the German Sustainable Building Council (DGNB). The authors found that even projects prioritising circularity struggled to meet quotas for reused or recycled materials.
Circular economy in the built environment is still in its infancy, with much of the information and social infrastructure still missing. Willing project developers often find it difficult to source second-hand materials in large volumes, store them until required, and ensure that the reclaimed materials meet safety and quality standards.
There are companies bridging these gaps by connecting supply and demand, but they are few and far between. Still, "there is no reason not to do it," argued Concular's Campanella. With over 400 examples, his company has shown that building with reclaimed materials is economically possible, faster, of equal quality (achieved through product re-certifications), and that volumes exist.
Changing supply chains
Thinking about circularity's potential and trade-offs holistically, systemically and across policy domains is needed to make the most of the economic model.
As the world decarbonises, supply chains change: while, for example, fewer demolitions are ultimately a positive development, the fact would also result in fewer reclaimed materials being available for new projects. Germany’s coal phase-out will have a big impact on the domestic supply of gypsum, the main constituent in plasterboard and a widely used construction material that is mainly derived from the plant's exhaust gases.
"We have to think about those interplays and knock-on effects, and how they operate within the wider system," Sheffield University's Gillott said. "As much as it is about getting the answer to what a circular future will look like and how to get there, it is about a deeper understanding of the solution space in which we will be required to operate."
Sharing finite resources
It is important to discuss what a sustainable built environment looks like for all stakeholders – from material manufacturers to the population as a whole – and to resolve the social, economic and cultural tensions in different locations, said Densley Tingley.
"That is massively going to shape what our material demand looks like in the future," she explained. "If we can only reach a certain circularity percentage, then we can have the conversation of where the rest of the materials will come from, and how we can get them in a decarbonised way."
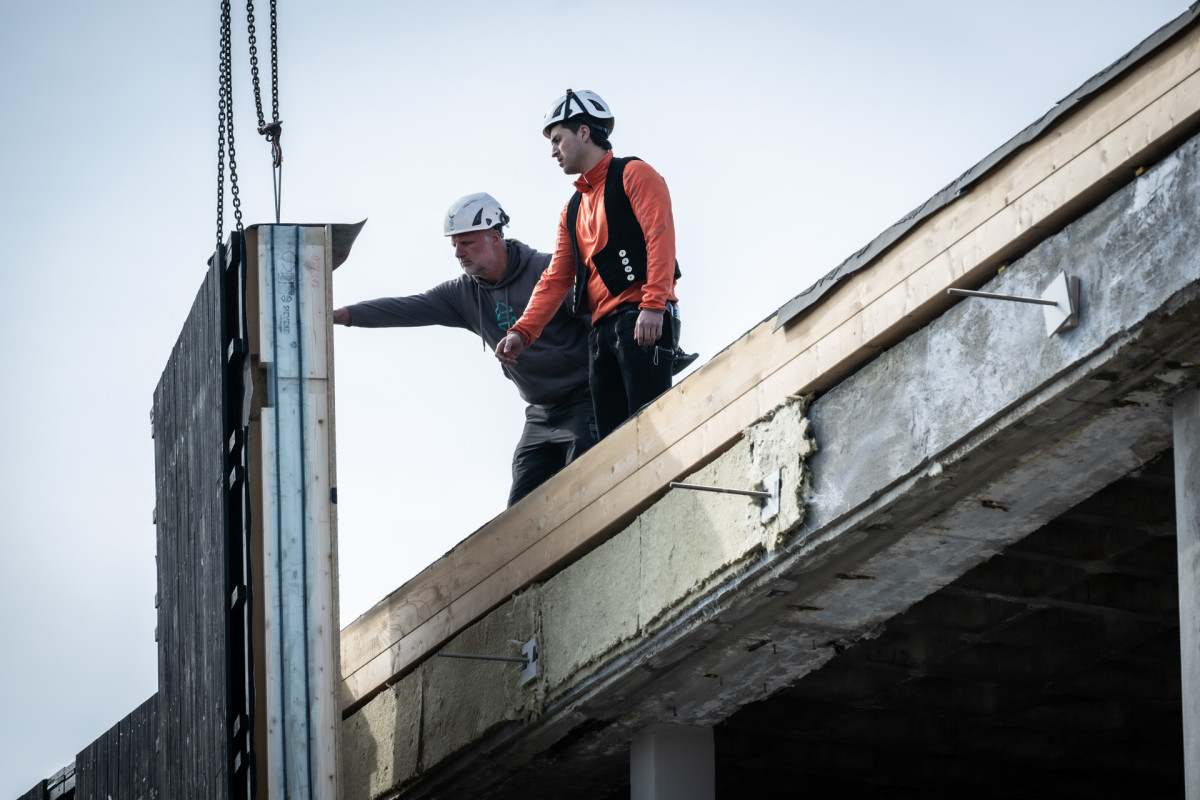
Urbanisation and population growth are set to increase the demand for housing and new buildings across the world. Under current International Energy Agency (IEA) projections, by 2070, the equivalent of the city of Paris will be constructed each week globally.
Indeed, the WGBC estimates that 75 percent of the infrastructure needed across the globe by 2050 is yet to be built. For Europe, however, the picture looks quite different: up to 95 percent of the bloc's buildings expected to be standing in 2050 already exist.
"We have done our development in Europe," said Densley Tingley. "We need to be mindful of what materials we are using and what we should be freeing up for others to use globally when we’ve got limited carbon budgets and limited resources."
This is highlighted by a 2021 WGBC flagship report: "There are simply not enough finite resources to carry on with the current take-make-waste consumption models," the authors concluded. "A transition to a circular approach is the only solution to balance international development and environmental goals."